Project Overview
The client requested a new floor coating system for a newly launched production line. The existing concrete required thorough surface preparation and durable coatings to withstand the demands of their operations. The biggest challenge was the tight 4-day timeline for completion, as similar flooring projects typically take 2-3 weeks.

About the Client
The client operates within the beauty and personal care industry, serving both established brands and emerging companies. They run facilities across the US, offering a wide range of products such as skincare, beauty products, hand soaps, OTC topical drugs, sun care, hair care, and fragrance items.
- 12 manufacturing facilities across the US, Canada, and Europe
- Over 3,000 employees
- 225 filling lines
- 4+ million square feet of space
Project Scope
- Size of Project: 20,000 sq. ft. of new production line flooring
- Location: Middlebury, Indiana
- Flooring System: HighWear epoxy-urethane system designed for demanding environments
Challenges
Existing Floor Conditions: The previous flooring had been used for past operations, and the coating had deteriorated over time. There were worn-out areas that needed patching, and the floor was overall in poor condition.
Time Constraints: The client required a completion timeframe of only 4 days, a much tighter schedule than usual, where projects of this scope would normally take 2 to 3 weeks.
Client Needs/Goals: The client sought a floor that would not only provide a fresh, modern appearance but also be easy to maintain and highly durable.
The Industrial Flooring Solution
Recommended Flooring Type: We recommended removing the old coating, resurfacing the concrete, and applying a high-wear epoxy-urethane coating. This system is ideal for multi-use manufacturing environments, providing both impact and chemical resistance to meet the client’s operational needs.
Design Considerations: The client wanted to retain the concrete look while ensuring it had the necessary resistance to stains and chemicals for longevity in their high-traffic manufacturing areas.
Customization: The customer requested a low-sheen finish with mild slip resistance to meet both aesthetic and safety requirements for their workforce.
Installation Process: Although this size of project would typically require 2-3 weeks, we leveraged a skilled workforce to expedite the process, completing the entire installation in just 4 days to meet the client's strict timeline.
Implementation
- Project Timeline: The project began with an initial consultation, followed by a quick scheduling and design phase. With the project timeline tightly compressed, Preferred, Inc. - Fort Wayne was able to deliver the floor in just 4 days from start to finish.
- Challenges Overcome: During installation, we learned that a concrete pit would be added by a separate contractor after our work had begun. We collaborated closely with the general contractor to devise a solution that would allow us to finish the coating in a shorter duration while keeping up with the tight schedule.
Results & Outcomes
The new flooring significantly improved both the appearance and functionality of the client’s production space, streamlining operations while enhancing the overall aesthetic. The high-wear epoxy-urethane system boosted the floor’s durability, providing resistance to wear and chemicals, which not only reduced the need for frequent maintenance and repairs but also promised long-term cost savings for the client.
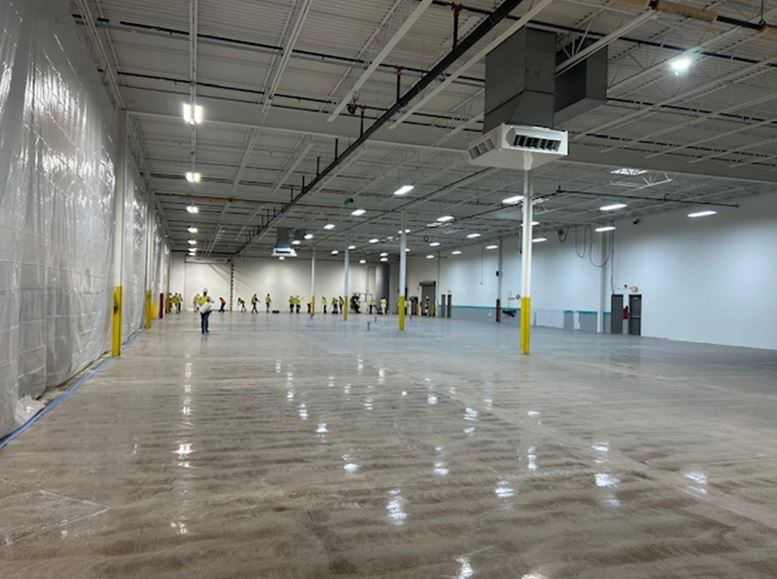