Surface Preparation & Cleaning Before Painting
PART 6
A wide range of surface preparation processes come together in a project depending on the surfaces to be painted. Many require specialized equipment and they must be handled carefully to get the best results.
The main purpose of preparation is to remove old paint and ensure a uniform surface. It can be a long process and is a major cost driver in a project. That said, clients should avoid the temptation to do any surface preparation on their own. Even if the right processes are applied to the right surfaces, it’s easy to overlook details that can come back to haunt you. At Preferred, we’ve often had to redo surface prep processes after clients try to chip in. This can add weeks to your timeline, not to mention costs. The bottom line: Don’t do it!
Focus your energy on verifying you lockout-tagout (LOTO) all appropriate equipment so it doesn’t turn on during work.
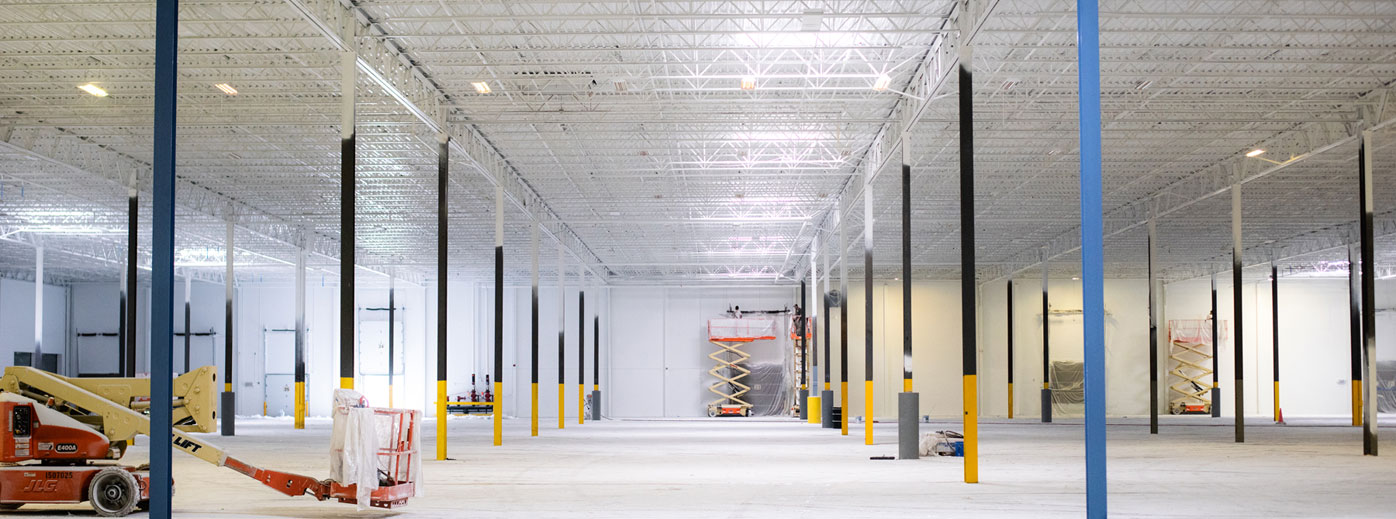
What Surface Preparations Are Used Before Painting?
The surfaces being treated and the materials being applied dictate preparation needs. Professional standards include many different types of preparation. Each one has its own equipment, costs, and use cases – some projects might use only a few or just one type of preparation.
These steps are the foundation that ensures your paint job will look great and last longer.
The major techniques to look for include the following:
- Steam and High-Pressure Cleaning: Pressure washing is used to prepare exterior surfaces before painting. The same equipment often has steam settings – these are used to prepare machine surfaces. Dry vapor (a high temperature, low moisture vapor) is used to clean and sanitize surfaces while eliminating build-up that can affect performance.
- Solvent Degreasing: Solvent degreasing prepares metal parts for painting. It’s also used to support other operations, like electroplating. A specialized machine turns soap into a foam that is precisely sprayed on and then rinsed off. It can be used on interior walls and machinery.
- Water Blasting: Water blasting uses high-pressure water to clean surfaces. It is more powerful than pressure cleaning and removes a thin layer of the original surface material along with dirt and grime. This can ensure that the surface is more uniform when it is time to apply materials. It is most frequently used to remove loose paint from exterior siding, tanks, and blocks.
- Soda Blasting: Soda blasting exposes a surface to sodium bicarbonate particles propelled with compressed air. The result is a very mild abrasive cleaning. Because the particles are so absorbent, they can often remove stubborn contaminants. Soda blasting is gentle enough for plastics, chrome, and glass. A high-pressure wand is used to carefully direct the flow and effect detail cleaning. This is the only option for more sensitive equipment and machines, but it does take longer. If there’s any concern about protecting a particular piece of equipment, this is the way to go.
- Sandblasting: On the other end of the scale, sandblasting is the most abrasive form of surface preparation. It can be used on walls and ceilings either inside or outside. It is great at removing paint, especially on concrete surfaces. It can also be used on tanks.
- Dry Ice Blasting: Dry ice is solid carbon dioxide. It is used in many different products, especially to keep produce cool during transportation. That said, it can be dangerous to work with, so your employees should steer clear. It is mainly used on ceilings and machines to remove loose paint.
How To Know You’re Getting The Right Surface Preparation For The Job
If the wrong preparation is used for any surface, the damage can be severe. In the worst scenarios, your equipment might require repair or replacement.
The information above will serve as a useful guideline, but it’s still important to ask questions of your contractor and ensure they’ve thought through the process.
Many forms of surface prep are potentially harmful to people, equipment, and other assets. In general, contractors should always choose the least abrasive surface prep that can get a job done in a reasonable amount of time. The surroundings should also be considered.
Always ask the following questions:
- “Could this harm any of our equipment?”
- “Is it bad for our employees in the area?”
- “How are you going to clean this up?”
Even when a surface prep isn’t very hazardous in and of itself, it’s important to be alert to the complications that can arise during cleanup. No matter how long preparation takes, cleanup might leave an area inaccessible for a period of time.
Contractors should be careful to apply the right media and aggregate for the situation. No option is perfect, and there’s bound to be some inconveniences – but the contractor should be able to explain the reasoning behind any selection.
Surface Preparation: Right Way, Wrong Way
- Jim looks for ways to perform surface preparation in-house. It costs him dearly to get the equipment and, thanks to lack of experience, a lot of treated surfaces get damaged. Since no time was spent verifying that dangerous equipment was secured, Jim narrowly avoided a big accident.
- Rob works with the teams on his factory floor to be sure lockout-tagout (LOTO) has been done for all hazardous equipment. He knows which questions to ask his contractor and makes sure he understands the communication and cleanup procedures that will keep things safe.
Remember:
- Although you can’t prep surfaces yourself, you can verify work your contractor does.
- Asking the right questions will ensure your project is as safe and efficient as it can be.
- It’s your responsibility to lockout-tagout (LOTO) equipment that could be hazardous.